You know those big blue Ikea bags? I’m sure you’ve seen people using them all the time – carrying groceries, as a beach bag, for storage, garden waste bags, or even for dirty laundry.
Well these bags are made from a super versatile and durable material called polypropylene. And because of its unique properties, they are perfect for a variety of uses and can be seen in daily applications.
Today we’re going to take a deeper look into this magic material is and answer some basic printing questions like whether it is safe to heat press polypropylene or iron on it, the recommended type of methods you can use, and I’ll even cover some best practices to avoid mishaps when dealing with this magic material. Read on.
So what is polypropylene?
Short answer – polypropylene (PP) is a thermoplastic polymer, which means it’s a form of plastic. It is also a polymer which is a big molecule that’s made up of smaller molecules joined together like a chain.
Polypropylene is a tough material and can withstand wear and tear. It is translucent, resistant to moisture and chemicals, extremely lightweight, and has a melting point of 160° Celsius or 320° Fahrenheit – keep this in mind when we discuss printing options later on.
Polypropylene is also affordable which makes it a popular choice for manufacturers.
What is polypropylene commonly used for?
Just look around and you’ll see PP everywhere – plastic packaging, parts for machinery and equipment, medical devices, toys, automotive parts, stationery and office supplies, construction materials, furniture and even fibers and textiles like those Ikea bags.
What does polypropylene mean to you?
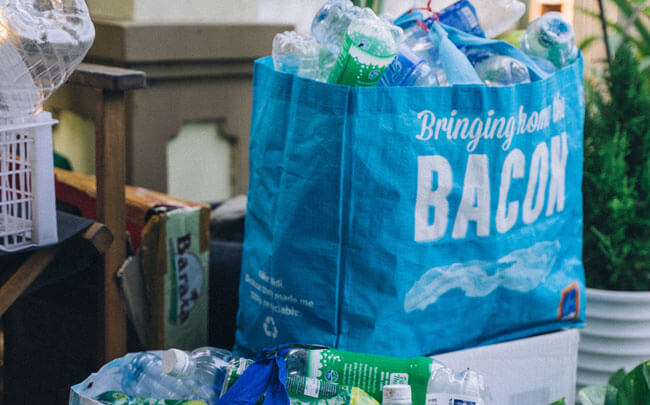
A lot of us heat press printers are always looking to expand our product line beyond the traditional cotton t-shirts. And polypropylene bags may just be the answer.
There are endless types of PP bags you can choose to print on – totes, supermarket bags, drawstring backpacks, cake cases, bottle bags, messenger bags, and even industrial bags for packaging bulk coffee, rice and other dry foods.
Today, these types of bags are all commonly made with what we call non-woven polypropylene, or NWPP for short. NWPP is a synthetic yet eco-friendly plastic fabric that provides an economical alternative to natural fibers like cotton, silk, or coconut husks.
The process of making these bags is the same as making regular cloth bags made of cotton or wool. But instead of using cotton threads, NWPP bags use threads made out of PP and are bonded together with heat. The finished NWPP fabric is soft to the touch and doesn’t feel like plastic at all. Amazing right?
6 Tips to heat press polypropylene bags
Here are a few tips to know before you start to heat press polypropylene bags.
1. Temperature
As I mentioned earlier, the melting point of polypropylene is 160° Celsius or 320° Fahrenheit. And as adaptable as this material is to harsh conditions, I would stay well below that limit if you’re going to apply heat to it.
Not all PP bag material is created equal – some are woven, some are non-woven, some are laminated, some are not – it’s best to check with the supplier the exact material you’re getting.
Regardless, I would set 150°C or 300°F as the max limit. The lower the temperature, the further you are from experiencing any warping, shrinking, or melting.
2. Pressure and Time
Keep in mind that even when you’re pressing well below the temperature limit, the amount of pressure and duration will affect the overall outcome.
Always consult the manufacturer’s recommended settings for heat transfers and always choose light pressure if possible. This is about 28-32 psi if you have a digital pressure reader. For doing it by feel, light pressure will mean you’ll be able to close the heat press lid with just one arm without using much force. At the most, you can go for medium pressure, but make sure the temperature is way under 135° Celsius or 275° Fahrenheit.
Read more: Heat presses with digital readouts can help with consistent output. Here are more heat press features that will help simplify your business.
3. Heat transfer paper
Depending on your heat transfer method, try to use transfer papers that have been designed specifically for low temperature items. Forever’s laser printer transfer paper for darks have been a staple of mine and many printers for years. This weedless transfer paper works well with dark colored PP bags, and has a good hand and impressive washability.
READ: Heat Transfer Paper Types and How to Find the Best One
4. Hot, Warm, or Cold Peel
Even if you’re sure to get brilliant print results with a hot peel heat transfer, I would stay away from them for polypropylene bags. As I previously wrote about the differences, hot peel papers transfer at roughly 300-400° degrees Fahrenheit and this would put it at its max temperature.
For a safer bet, go with warm peel heat transfers. Not only do they offer the best of both worlds (hot and cold), but it also reduces the risk of melting or scorching the PP bag while retaining print quality and durability.
5. Teflon cover sheet
Using a teflon cover at all times is just good practice. It can protect your heat press’ top platen from ink smudges, dirt, or melted vinyl, and make cleaning less of a hassle. And since teflon covers have a high temp resistance up to 600° Fahrenheit, it will protect your pp bags from overheating.
6. Heat Press Pillow
By slipping a heat press pillow under the PP bag, you can instantly create a raised surface. This not only allows you to apply even pressure across the printed area, but the rest of the pp bag that isn’t getting printed will not come into contact as much with the heat – reducing the risk of melting.
You can use teflon covers for all heat press printing method including heat transfers and sublimation.
Final Thoughts
If you are still feeling intimidated with heat pressing PP bags, you can always perform a test first with a sample. Remember to keep the temperature low so you can identify what works for you and you will avoid a messy, melted bag.
If you’re planning to buy pp bags and blanks from a supplier, read this article first to avoid costly mistakes.